α高強石膏粉工藝介紹
隨著科學技術(shu)的迅速(su)發展,α型高強(qiang)石膏(gao)的應用領域日趨(qu)廣(guang)泛(fan),已(yi)涉及航空(kong)、汽車、橡膠、塑料、船(chuan)舶、精密鑄造、高端建材、工藝美術(shu)、3D打(da)印、醫療等多種領域,而且(qie)產品也趨(qu)系列化。
目前高強石(shi)膏生產工藝主(zhu)要有以下幾(ji)種(zhong)方法:
● 蒸壓(ya)法(fa)(fa)(一步法(fa)(fa)、兩步法(fa)(fa)、半干蒸壓(ya)法(fa)(fa))
● 水熱法(fa)(加壓水溶液法(fa)、常壓水溶液法(fa))
高強石膏生產工藝(yi):
蒸壓法:二水(shui)石(shi)膏在一定壓力的飽和(he)蒸汽介質中脫水(shui)生(sheng)成α型高強石(shi)膏
水(shui)熱法:二水(shui)石膏(gao)在某(mou)些(xie)酸類(lei)、鹽類(lei)水(shui)溶液中通過加熱蒸煮生(sheng)成α型高強石膏(gao)
1.(蒸(zheng)壓法(fa))生產α型高強石膏:
(1)一步法;
一(yi)步蒸壓法是(shi)一(yi)種傳統(tong)(tong)的(de)生(sheng)產α型高強石(shi)膏的(de)生(sheng)產工藝。一(yi)定(ding)粒(li)度的(de)原料(liao)在含有一(yi)定(ding)壓力、飽和蒸汽的(de)蒸壓釜中脫水后(hou),在蒸壓釜中繼續(xu)干燥(zao),干燥(zao)完成后(hou),經粉磨系統(tong)(tong)將(jiang)石(shi)膏塊(kuai)粉磨成一(yi)定(ding)細度的(de)石(shi)膏粉,再經包裝(zhuang)系統(tong)(tong)包裝(zhuang)入庫。
一步法(fa)的(de)生(sheng)產(chan),使石(shi)膏的(de)脫水(shui)和烘干在同一設備中進行,避免了(le)再(zai)生(sheng)石(shi)膏的(de)生(sheng)成(cheng),保證了(le)高強石(shi)膏粉質量的(de)穩定性。
蒸壓釜(fu)具有石膏脫(tuo)水和烘干兩種功能,烘干熱(re)源可(ke)采用(yong)導(dao)熱(re)油間(jian)接換熱(re)或熱(re)風直接換熱(re)烘干。
要求原料具有(you)一定(ding)粒度,適用(yong)于(yu)天然石膏或經造粒后的工(gong)業副產石膏
(2)二步法
二步蒸(zheng)壓(ya)法也是一(yi)種傳統(tong)的生(sheng)產α型高強(qiang)石(shi)膏(gao)的生(sheng)產工藝。一(yi)定粒度的原料在含(han)有(you)一(yi)定壓(ya)力、飽和蒸(zheng)汽的蒸(zheng)壓(ya)釜(fu)中(zhong)脫水后(hou),物料從蒸(zheng)壓(ya)釜(fu)中(zhong)放(fang)出進(jin)入干燥(zao)設備,干燥(zao)完成(cheng)后(hou),經粉磨系統(tong)將(jiang)石(shi)膏(gao)塊粉磨成(cheng)一(yi)定細度的石(shi)膏(gao)粉,再經包(bao)裝(zhuang)(zhuang)系統(tong)包(bao)裝(zhuang)(zhuang)入庫。
二(er)步(bu)法的生產,脫水和烘(hong)干(gan)在(zai)不同設備中進行,由(you)脫水工(gong)段進入烘(hong)干(gan)工(gong)段時,造(zao)成(cheng)壓降及溫降,使部分(fen)物料水化生二(er)水石膏,造(zao)成(cheng)產品強度(du)降低,影響產品質量,適(shi)用(yong)于低檔產品。
要求(qiu)原(yuan)料具有一定(ding)粒(li)(li)度,適(shi)用于天(tian)然石膏或經造粒(li)(li)后的工業副產(chan)石膏
(3)半(ban)干蒸(zheng)壓法(fa)
將粉狀(zhuang)或(huo)較小顆粒(li)與粉狀(zhuang)混(hun)合的石膏原料(liao)與轉(zhuan)晶劑(ji)溶液進(jin)行(xing)均勻(yun)混(hun)合,混(hun)合后原料(liao)總體含水率較低的半(ban)干(gan)狀(zhuang)態,將半(ban)干(gan)狀(zhuang)態的石膏原料(liao)直接進(jin)入(ru)轉(zhuan)晶設備,在一定壓力的飽(bao)和(he)水蒸汽介質下進(jin)行(xing)轉(zhuan)晶或(huo)造粒(li)后進(jin)行(xing)轉(zhuan)晶的方法稱為半(ban)干(gan)蒸壓法。
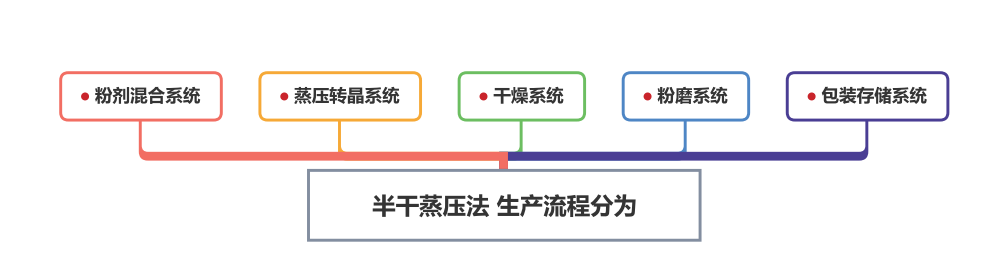